Every application that requires springs will need to ensure they have one made of the highest quality materials and with the best processes to be successful. The quality of these initial processes and their instigating designs will dictate the longevity of the springs and, potentially, the success of their application.
Failed machinery, equipment or tools will have a huge impact on the productivity of your business and create significant downtime as you repair or replace the internal components. For example, as spring manufacturers, we know many applications require high-quality springs to function. Read on to learn how we maximise their life cycle and provide springs you can rely upon for many years.
What Affects a Springs Longevity?
During spring design, details about the product’s application are essential. This will relate to several factors, including load stress, operating friction and environmental conditions.
Springs need to work with predetermined loads to function reliably. Installing springs erratically will lead to unpredictable results as these components work with stresses outside their established parameters. Additionally, springs under too much pressure will compress more than intended and increase the likelihood of it failing or breaking.
Friction is also a concern regarding spring conditions. If a badly designed spring is installed in the wrong location, it may generate friction as it compresses and relaxes. This will produce similarly unpredictable spring operations and increase wear on the spring and the installed area, creating permanent damage to both.
The environment in which the spring will operate is important as it may limit the intended function or significantly decrease the life cycle of this component. Specific treatments are designed to make springs effective in predetermined environments and must be added to ensure the spring functions adequately. The main conditions to consider are temperature and contaminants. Additionally, electronic springs may potentially be exposed to harmful magnetic fields.
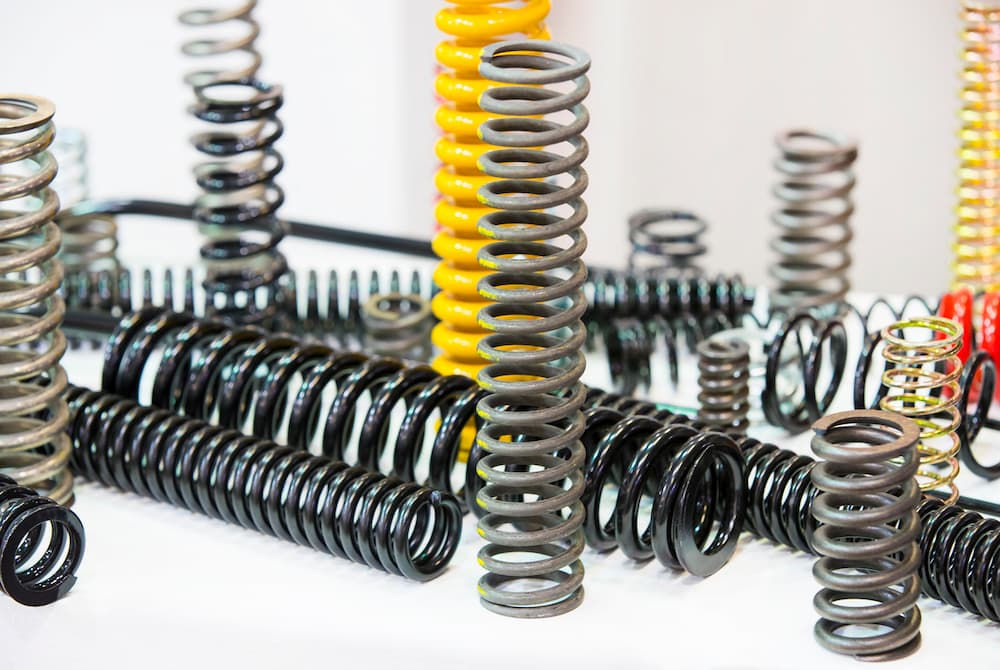
Methods to Lower Spring Stress
As an experienced small spring manufacturer, we have created millions of springs for many different applications, each requiring unique specifications regarding materials, processes and finishes. Here are some approaches that significantly increase the life cycle of spring.
Operational Considerations
Lowering the stress inflicted on the spring is one of the best ways to extend its life. By taking steps to reduce stress, you can make sure you will never overload it, resulting in damaging pressure. This will be avoided by adapting your spring design with a larger wire diameter or lowering the final load to create more room for the spring to compress. Any additional internal pressures can also be reassessed and improved to support the spring’s operation.
Shock loading is severely harmful to a spring’s longevity; this is when the intended load or spring rate is increased dramatically in either weight, speed or frequency. An example of shock loading would be when a load is dropped at the height; the sudden increase in stress will potentially reduce the spring’s performance as permanent damage is inflicted. In addition, the increasing number of shock-loading events will significantly increase the potential of spring failure. Shock loading can be reduced by adding friction or vibration-dampening devices to absorb some of the pressure from the event.
Additional Treatments
Additional treatments are essential to increase a spring’s capabilities and resistance to environments. For example, an untreated spring will be at risk of damage when exposed to heat or humidity. Whilst keeping a spring cool will reduce this risk, treating your springs is far more effective.
In some specific applications, a spring will resonate if the machines operating speed or harmonics frequency has a similar natural frequency. In these cases, the spring’s design should consider the operating frequency and ensure it is no more than one-thirteenth of the natural frequency to avoid harmonising.
Shot peening is a commonly used process due to the effective results it produces. Shot peening creates compressive residual stresses on the springs as they are bombarded (or shot) with spheres made from either metal, glass or ceramic materials. These impacts create minute indentations on the metal springs and make the external material dense. The final result is a spring with a compressively stressed layer that improves the spring life cycle by five to ten times its estimate before the treatment. The stressed layer helps resist corrosion, cracking, fatigue stress and hydrogen embrittlement; all elements springs are exposed to and will potentially dramatically decrease a spring’s life.
Pre-stressing is an additional process affecting the whole spring, benefiting a spring design and extending its life. This additional manufacturing element uses higher solid stresses intending to raise the elastic limit torsionally.
Custom Springs Manufactured at Airedale Springs
At Airedale Springs, we manufacture the highest quality bespoke compression springs and wire forms. Our team of expert engineers will work with our clients through the entire process of spring development, from design, prototype and production, to make sure you receive the best springs for your needs. Contact us to discover how we can help with your next project.