When it comes to mechanical components, wire forms and springs have a crucial role in a wide range of applications. Both wire forms and springs offer unique characteristics and advantages depending on the specific requirements of a project, but knowing which one is the best choice is vital for designers to ensure the success of the finished product. Read on to explore the unique differences between these two components we manufacture here at Airedale Springs.
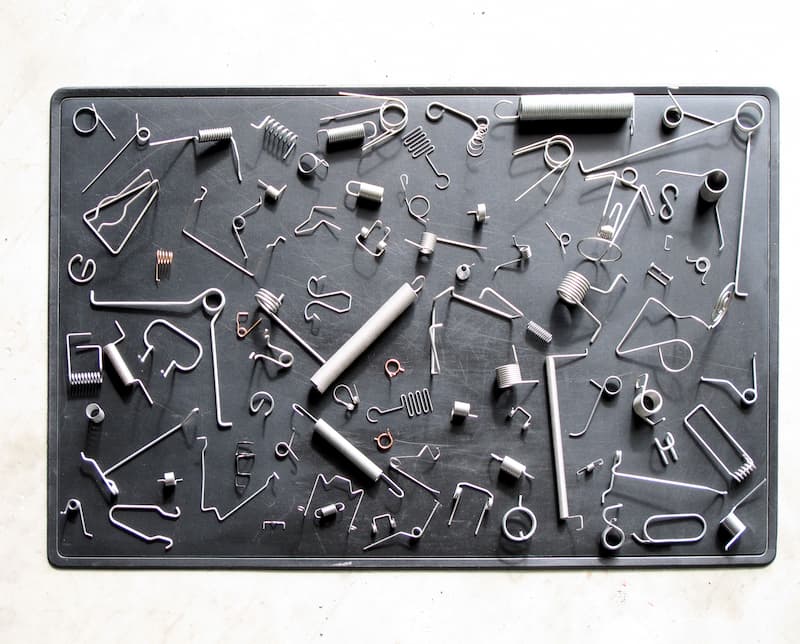
Wire Form Characteristics
Wire forms are made by manipulating wire into custom shapes through various manufacturing processes such as bending, cutting, or shaping. They are generally designed to fit specific applications requiring constant movement or flexibility.
This versatile component comes in various shapes and forms, including hooks, clips, and rings. Different wire forms may be used depending on the application’s requirements, each with unique properties and advantages. This versatility in design is the key characteristic of wire forms because where wire springs are designed to provide resistance to force, wire forms will offer more flexible movement in any direction.
At Airedale Springs, we specialise in creating high-quality wire forms in custom shapes and sizes, with our design service helping clients to find the optimal solution for their specific application.
Wire Form Applications
We have manufactured the highest quality wire forms in various sectors. For example, wire forms have many applications within the electronics sector. Here are a few examples of products that need wire forms:
- Pacemakers
- Ultrasound scanners
- Light fittings
- Battery contacts
- Telecommunications
Wire form manufacturers such as ourselves are essential to the continued production of hundreds of thousands of advanced electrical product designs, and we ensure all our wire forms will fit your required specifications perfectly.
Spring Characteristics

Springs are essential mechanical components that store and release mechanical energy. They are typically made from metal wire coiled into a helical shape to provide resistance to force, whether pushing against compression springs or pulling back from applied pressure.
Popular Spring Designs
Springs are manufactured through coiling, where the wire is wound around a mandrel or a cylinder to create the desired shape. There are several types of springs, each serving a specific purpose.
Torsion springs, for example, are designed to provide torque or rotational force when twisted. They are commonly used in applications like electrical switches or overhead garage doors.
Extension springs, on the other hand, offer resistance to stretching and are commonly found in trampolines, garage doors, and even surgical instruments.
Compression springs provide resistance when compressed and are widely used in automotive suspension systems, mattresses, and industrial machinery.
Flat springs differ in their form and function. Flat springs are thin strips of material that store mechanical energy when subjected to a bending force. They are typically used in applications where limited space is available and where a low profile is required. Aerospace, electronics and robotics are common applications that use flat springs.
Springs are highly regarded for their strength and durability, making them ideal for applications requiring constant force or tension. The versatility and reliability of springs make them a critical component in many industries, offering solutions for a wide range of force and tension requirements.
Spring Rate’s Relationship to Design
A spring’s spring rate, or stiffness, is typically defined as the change in force per unit displacement. In the case of compression springs, calculating the spring rate determines the force required to compress the spring, while for extension springs, it is the force needed to extend the spring.
However, the spring rate is not only limited to spring designs. Wire forms have some elasticity and will store and release energy differently.
For example, wire forms are used alongside small springs in electronics for electrical contacts that can have a specific amount of elasticity to maintain contact pressure. However, the spring rate calculation for non-spring wire forms differs from that of springs. It requires a more complex application of Hooke’s Law to provide a constant force/tension under different conditions and applications. The forces and deflections required for device functionality can vary widely in non-spring wire forms, and this should be considered for your design.
Which Is Best For Your Design?
When considering the applications best suited for wire forms and springs, comparing and contrasting their unique attributes is important. Let’s use the automotive sector as an example.
Wireforms, with their wire structure, excel in applications that require constant movement. Industries like automotive and aerospace greatly benefit from wire forms due to their flexibility and ability to endure repetitive motion. Wire forms are commonly used in suspension systems in the automotive sector, allowing vehicles to navigate uneven terrain and absorb shocks smoothly.
In contrast, springs are ideal for applications requiring constant force or tension, with the automotive sector often relying on springs to maintain consistent pressure or tension. Springs come into play in other components, such as valves, clutches, and brakes. Springs ensure proper operation and control by maintaining the pressure and tension required for optimal functioning.
Bespoke Designs from Airedale Springs
Choosing the right components is critical for any design’s success, and at Airedale Springs, we understand the importance of selecting the perfect springs or wire forms for your specific application.
As an experienced custom spring manufacturer and wire form manufacturer, we have been helping our customers for decades to take their products to market with reliably positive results faster. During our extensive spring design process, we carefully consider the characteristics and purpose of the spring to select the ideal size and other specifications that best suit our clients’ needs. With our assistance and expertise, you can be confident that your design incorporates perfectly-sized springs or wire forms that precisely meet your requirements.
Get in touch with us today, and let us help you make your next project a success.