Spring rates are an essential calculation that manufacturers need to master to produce custom spring products within various specifications. Furthermore, they all rely on Hooke’s law; the rate will differ for every type of spring and design to function correctly in their intended application. Read on to discover how a custom spring manufacturer like Airedale Springs calculates these spring rates for our range of products.
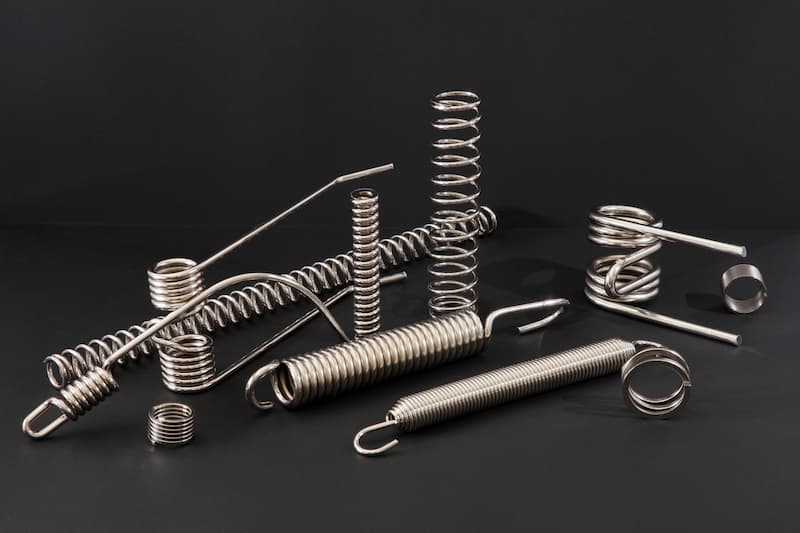
What Is a Spring Rate?
Many clients will ask, ‘How do you increase a spring’s stiffness?’. Although we have a great relationship with clients to understand what this means, within the industry and for most spring manufacturers, the correct term is spring rate.
Spring rate is a critical parameter in spring manufacturing because it determines the spring’s behaviour when subjected to external forces. The spring rate, or the spring constant, is the force required to compress or extend the spring a certain distance. If the spring rate is too low, the spring will not be able to support the required load, while if the spring rate is too high, the spring may become brittle and break under stress. In addition, the spring rate can be affected by various factors such as wire diameter, coil pitch, material properties, and the number of active coils. Therefore, accurate spring rate calculation is essential in spring design and analysis to ensure optimal performance and longevity of the spring.
Hooke’s Law: Origins of Spring Rate
In 1676, Robert Hooke made a ground-breaking discovery that revolutionised the field of physics concerning springs. Hooke’s revelation was that the force required to deform a spring further increases proportionally to the deformation already experienced. While studying the stress-strain curve, he arrived at this observation and noted that many materials exhibit a linear region.
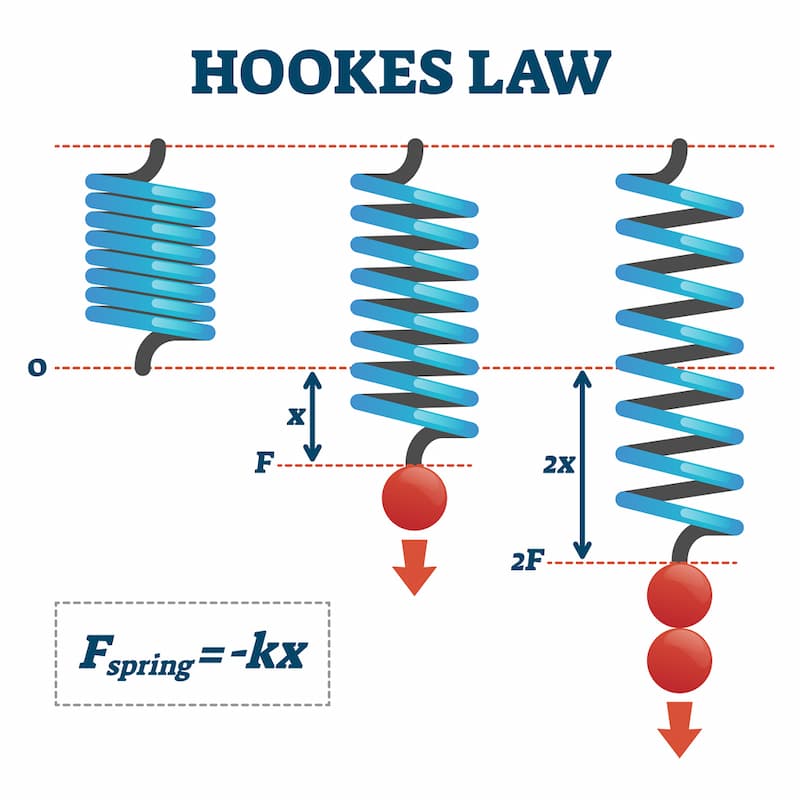
The force needed to deform a metal spring through stretching is proportional to the extension of the spring. This relationship is expressed algebraically as F = -kX, where F represents force, k denotes the spring constant, and X is the deformation or extension length. However, it is essential to note that exceptions exist to this rule. For example, if the spring is stretched beyond its elastic limit, it will no longer conform to Hooke’s Law. In such cases, measurements are taken at this point, and this length is considered the elastic limit of the spring. It is crucial to consider the elastic limit of the spring to avoid overstressing it, which could lead to permanent damage or breakage.
Hooke’s law is the origin of spring rate science and is a cornerstone of spring engineering. It is used to design and analyse various springs, including compression, tension, and torsion springs. While each spring design is unique, all the rates will be calculated by determining the force required to manipulate the spring one unit of length, typically measured in newtons per millimetre (N/mm) or pounds per inch (lbs/in).
Compression Spring Rate
A compression spring manufacturer will calculate the spring rate of a compression spring by measuring the wire diameter, mean coil diameter, and the number of active coils. The mean coil diameter is calculated by adding the inside diameter of the spring to the wire diameter and dividing the result by two. The number of active coils is calculated by subtracting the number of inactive coils (usually the two at the ends) from the total number of coils.
Once the measurements are taken, the spring rate can be calculated using Hooke’s Law formula:
F = kX
F is the force applied, k is the spring rate, and x is the displacement.
For compression springs, the displacement is equal to the difference between the free length of the spring and its compressed length. Therefore, the spring rate can be calculated by dividing the force applied by the displacement.
It is important to note that several factors can affect the spring rate, including the material properties of the wire, the diameter of the wire, and the number of active coils. Therefore, precise measurement and calculation are crucial to ensuring that the compression spring is designed to meet the application’s specific requirements.
Tension Spring Rate
As a tension spring manufacturer, we calculate the spring rate of a tension spring and determine specific parameters similar to the compression springs (the wire diameter, mean coil diameter, etc.)
Once the measurements are decided, the spring rate is calculated using the following formula:
k = (Gd^4)/(8ND^3)
k is the spring rate, G is the shear modulus of elasticity of the material, d is the wire diameter, N is the number of coils, and D is the mean coil diameter.
The shear modulus of elasticity is a material property that indicates how resistant a material is to shear stress. It is worth noting that, once again, similarly to compression springs, several factors will affect the spring rate, such as the previously mentioned spring materials, diameter, and the number of active coils.
Torsion Spring Rate
To calculate the spring rate of a torsion spring, a torsion spring manufacturer needs to determine the previously mentioned initial parameters. Once those measurements are dictated, the spring rate is calculated using this formula:
k = (Gd^4)/(32Nc)
k is the spring rate, G is the shear modulus of elasticity of the material, d is the wire diameter, N is the number of coils, and c is the coil diameter.
The spring rate can also be calculated using the following formula:
k = (T/θ)
Where T is the torque applied to the spring, and θ is the angular deflection of the spring.
Although this spring’s unique design is compared to compression and tension springs, its rate will also be affected by the material factors already mentioned.
Spring Design and Manufacturing at Airedale Springs
Choosing Airedale Springs as your spring and wire form manufacturer provides you with our extensive experience and commitment to quality. With over 70 years of experience in the industry, we have built a reputation as a leading manufacturer of high-quality springs for various applications.
As a custom spring manufacturer, our team of experts is dedicated to providing custom spring solutions that meet the specific requirements of our clients, including the demanding specifications for electronic springs.
Contact us to discover how our engineers can help you with your next application.