Most springs share a common goal – they’re manufactured to store and release energy as required. Many materials on paper can perform this task (including paper itself, although we wouldn’t recommend it), but not all springs materials are created equal. When determining what spring you need for your required application, it’s essential to consider the material your spring is made from. Today we’re going to look at non-ferrous alloys and how we use them in spring manufacturing.
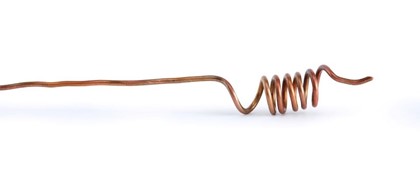
What Are Non-Ferrous Alloys?
The word ferrous means ‘containing or consisting of iron’, so for metal or alloy to be non-ferrous, it naturally means that it doesn’t contain iron. Since non-ferrous metals don’t include iron, they are not magnetic and will not rust.
The most common group of non-ferrous metals, which we use most in our spring design, are copper-based alloys. We also work regularly with nickel and aluminium alloys. As pure metals, these materials often don’t possess the required properties for good spring manufacturing. Aluminium is malleable, and copper is soft and ductile – but when alloyed, their properties are strengthened, and they become excellent candidates for certain spring applications.
What is the Difference Between Ferrous and Non-Ferrous Metals?
As mentioned above, ferrous metals are those which contain iron, and non-ferrous metals don’t. Ferrous and non-ferrous metals each have distinct properties that make them suitable for different applications. Whilst ferrous metals are prized for their strength and durability, the high carbon count means they are more susceptible to rusting when exposed to moisture. Non-ferrous metals, on the other hand, have a lower carbon count, often meaning they are corrosion resistant and can be used in environments where ferrous metals like steel would not be suitable.
When an application calls for a non-magnetic, corrosion-resistant metal, for example, in electronics, this is when non-ferrous metals perform best.
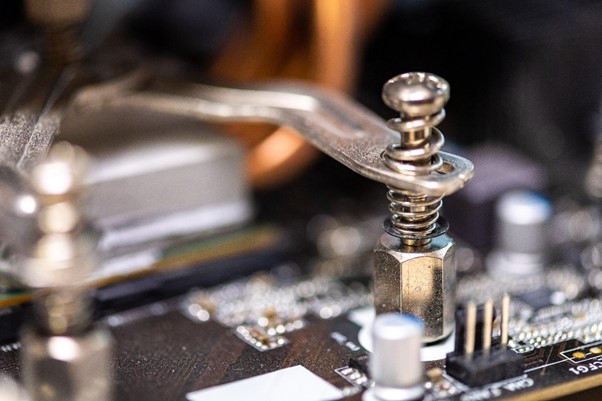
Common Non-Ferrous Alloys in Springs
As spring manufacturers, we work with several non-ferrous alloys, producing springs for many different industries. Here are three of the most common non-ferrous alloys we regularly use to achieve strong, high-quality springs:
Aluminium
At a third the weight of steel, aluminium is an incredibly lightweight metal and resists corrosion well. These are valuable properties for many applications, including industries like aerospace. Alone is it pliant and weak compared with other materials. However, when alloyed with other materials or put through certain processes like cold working, it can be strengthened to meet the demands of harsh environments. You will often find aluminium alloyed with magnesium and silicon to produce tough yet lightweight springs.
Nickel
Nickel is well known for maintaining strength at incredibly hot and cold temperatures and good solderability and thermal conductivity. It’s tough and ductile, which is why you’ll find nickel springs in the most extreme environments. Nickel alloys are often used when the strength of stainless steel doesn’t meet the demands of the application. Popular alloys include nickel-copper, nickel-chromium and nickel-iron.
Copper
Copper is a soft, malleable metal with high thermal and electrical conductivity – which is why you’ll mainly find copper springs used in electrical applications. By alloying copper with other metals like zinc (which makes brass), tin (bronze) and beryllium, the properties of copper can be adapted and tweaked to fit almost any application.
Applications for Non-Ferrous Springs
The wide variety of non-ferrous metals available for use in spring manufacturing means they suit a diverse range of applications. Nickel’s toughness, tolerance to high and low temperatures and corrosion resistance make it well suited for spring application in harsh environments like oil rigs and around chemicals.
Copper alloys are widely used in electronic springs and wire forms due to copper’s excellent electrical conductivity and relatively low weight. You’ll also find copper in musical equipment, industrial machinery, roofing, valves and tools.
The lightweight nature of aluminium, coupled with its ability to reflect radiant energy and resist corrosion, make it an excellent choice for springs required for aerospace, marine and railway applications. You’ll also find it in bicycles, motors and generators.
The many available alloys of non-ferrous metals make it possible to adapt and manipulate the properties of the metal to suit your requirements. They tend to be more expensive than their ferrous counterparts – but it’s a worthwhile price to pay to get the correct spring for your desired application.
Industries that Benefit from Non-Ferrous Springs
As discussed, springs manufactured from non-ferrous metals and their alloys have multiple applications across many industries thanks to the versatility of the alloys. In summary, non-ferrous alloy springs are commonly found in:
- Marine Sector
- Chemical Plants
- Electronics
- Aerospace
- Oil Rigs
We hope you enjoyed this look at the versatile nature of non-ferrous metals and how we here at Airedale Springs use them in our manufacturing. As expert spring manufacturers, we understand the importance of choosing the right material for your spring requirements. If you would like any more information about the materials we use for our springs and wire forms, get in touch with us today and see how we can help.